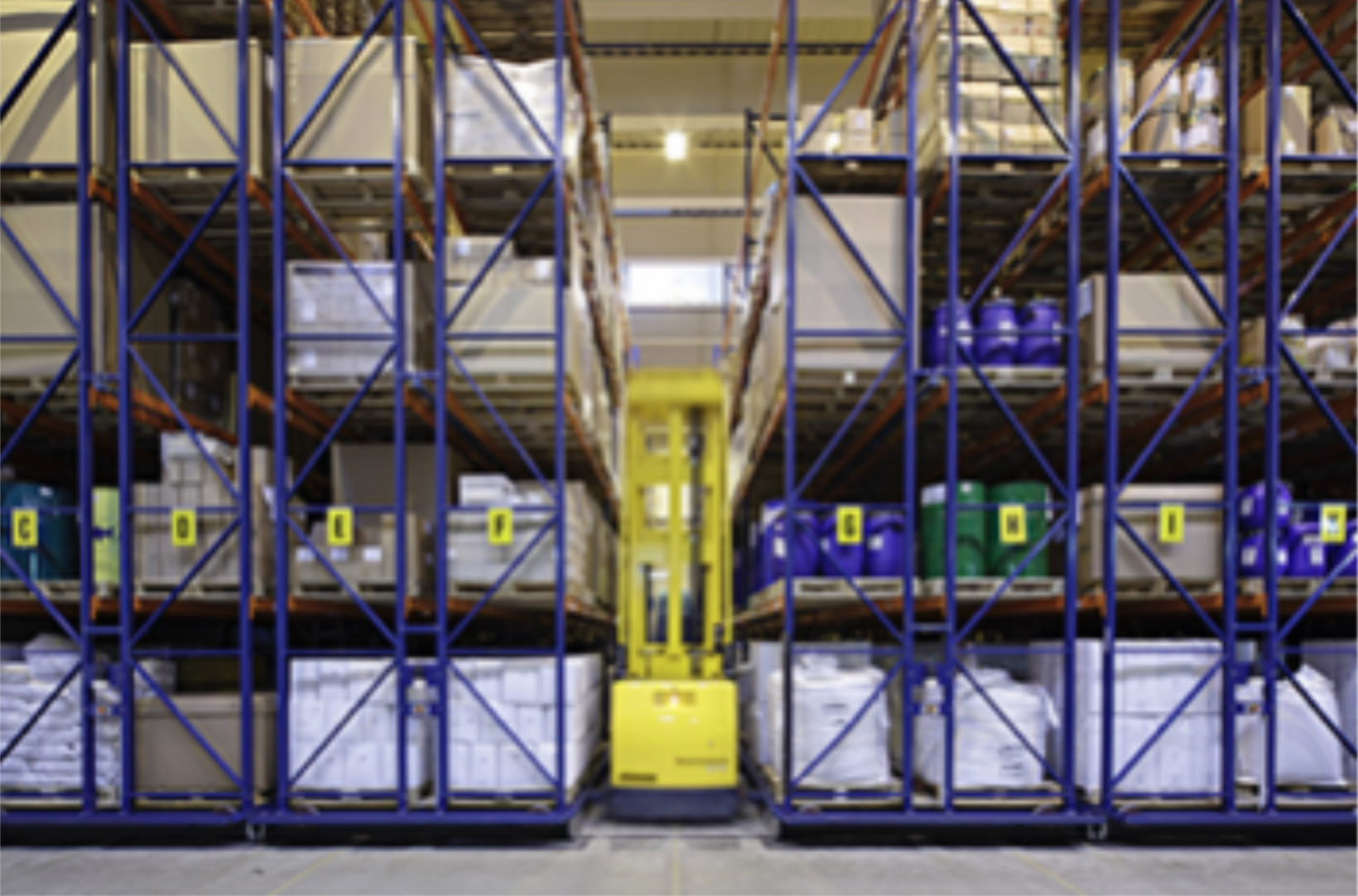 |
Warehouse, space for 2’500 palettes Approx. 800 different raw
materials, Temperature and humidity are
monitored, ERP-system controlled, full traceability
|
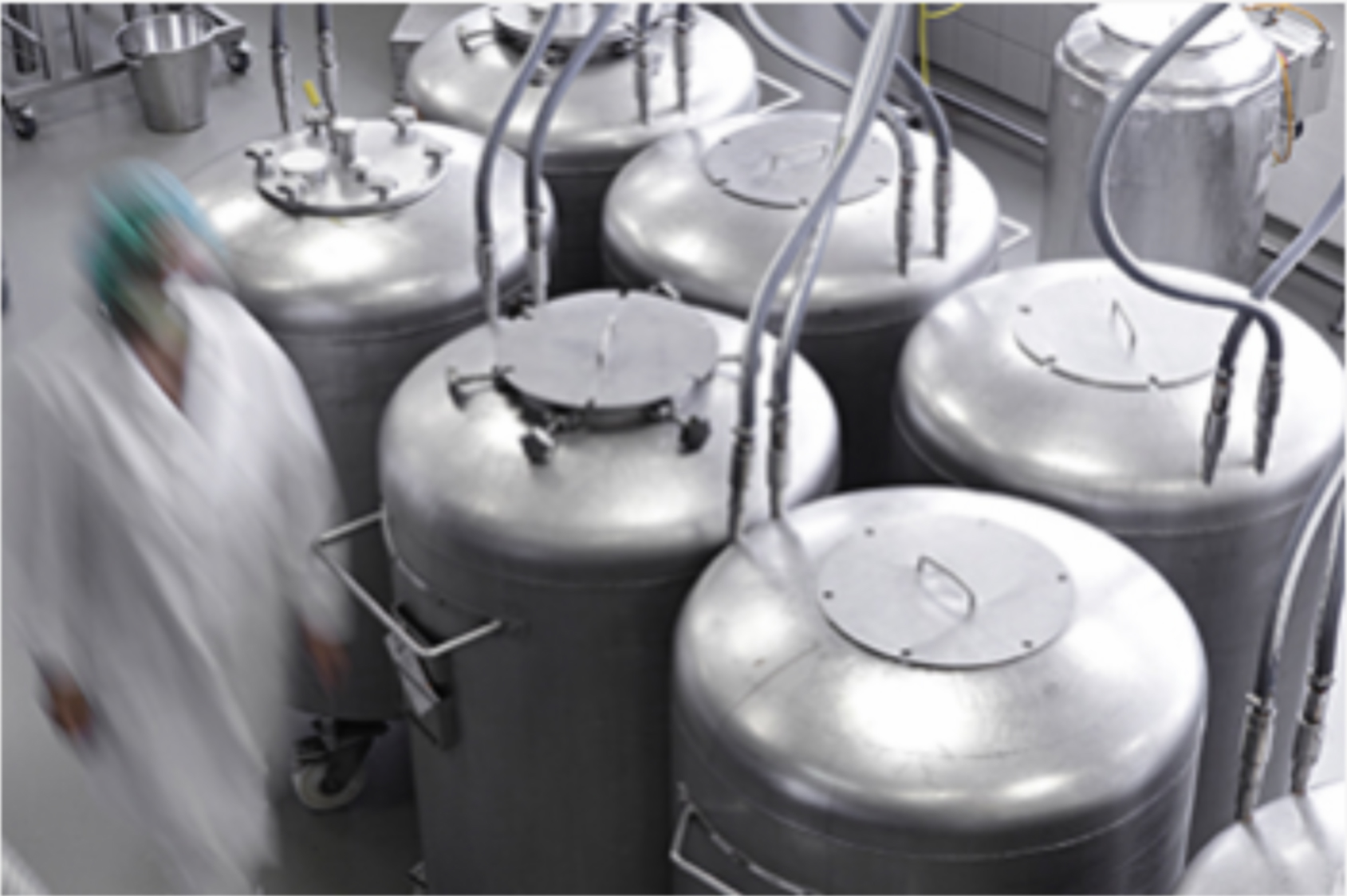 |
Gelatin preparation, intermediate storage tanks, addition of
colorants and flavors possible, all manufacturing steps are
monitored and controlled by ERP-System, full traceability
Raw granular gelatin is mixed with glycerine and water. Coloring
agent can also be added at this stage. Glycerine acts as a
plasticizer in the gelatine compound. Other plasticizers can also be
used either alone or in combination with glycerine, such as
sorbitol. The proportions of each ingredient involved in the mixture
should be considered carefully because the shell material needs to
be adapted to formulation and/or environmental requirements. For
instance the gelatin recipe may need to be adjusted to account for
acidity, water content of the fill material or high humidity
environmental conditions.
|
|
Fill mass preparation, steel tanks, intermediate storage tanks,
GMP environment.
A homogeneous fill material plays a vital role to ensure the
uniformity of each Softgel dose. Various equipment should be
available, such as processing tanks, high-shear mixer, homogenizer
and variety of mills is use.
|
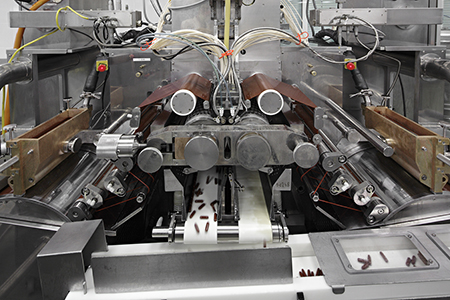 |
Encapsulation machine, encapsulation part (“heart” of encapsulatin
machine) Temperature and humidity are
monitored, ERP-system controlled, full traceability.
Encapsulation is the manufacturing process that brings the gelatin
shell and the fill material together to form Softgel capsules. It
takes place in a closed environment where the relative humidity is
around 20%. The gelatin shell and fill material are brought together
simultaneously in the encapsulation machine.
|
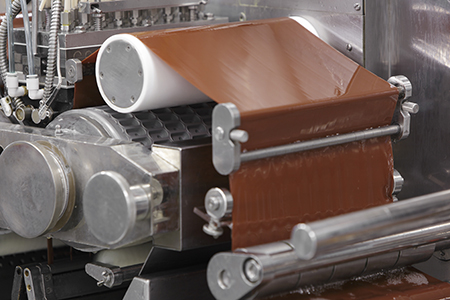 |
Encapsulation machine, gelatin ribbon. Temperature and humidity
are monitored, ERP-system controlled, full traceability.
A pump delivers the warm gelatin over two chilled drums which are
located at both opposite sides of the machine, through a spreader
box that sits over each drum. The warm liquid gelatin flows over the
drums and this transforms the liquid gelatin into two solid ribbons
of gel. The left and right ribbons pass over rollers which feed them
through two die rolls. These die rolls determine the shape and size
of softgels and cut the Softgel shell from the ribbons as they turn
around.
|
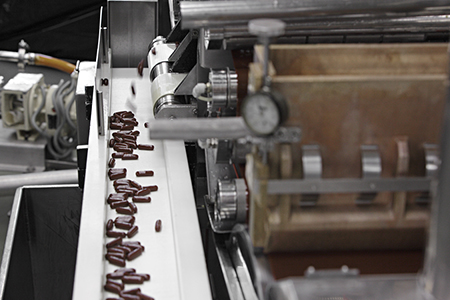 |
Encapsulation machine, converter ribbon from encapsulation machine to
drying tumbler.
Temperature and humidity are monitored, ERP-system controlled,
full traceability.
Performed by a tumble dryer. Tumbler drying the softgels to removes
approximately 30 percent of the water content in the softgel
capsules.
|
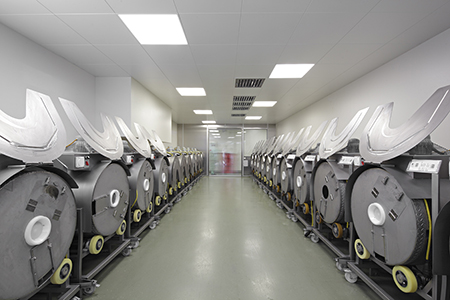 |
Drying room, drying tumbler
Temperature and humidity are monitored, ERP-system controlled,
full traceability.
Softgel capsules are transferred to the drying room where high air
flow exists and they stay around 24 to 48 hours or until the
softgels become hard enough
|
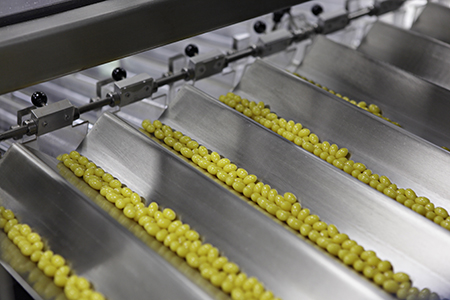 |
Calibration and sorting
Temperature and humidity are monitored, ERP-system controlled,
full traceability
Fully automatic softgel sorting machine equipped with electronic
sensors is used to sort and remove the damaged, misshaped, broken
etc. gelatin capsules,
Afterwards manual visual inspection takes place. Any misshaped,
damaged and/or not fully filled capsules are removed manually by
using an inspection table.
|